The OLD Using MOSFETs Page
This page is dedicated to learning about MOSFETs in DC motor
control.
Note: the descriptions on these pages are still valid for educational
purposes only. A better MOSFET
design is shown at
index.html
(April 2001)
A short MOSFET
primer
MOSFETs is an abbreviation for Metal Oxide Field Effect Transistors.
They are transconductance devices which is a fancy way of saying that a
voltage on the input (gate-source) causes a current to flow on the output
(drain-source). They have a very high input impedance in the 10s of mega
ohms which is very desirable. The high input impedance means that there
is very little power required to turn a MOSFET on.
MOSFETs have a threshold voltage that must be reached in order to turn
them on. It is called Vgs(TH). Usually somewhere around 4.5V to 7V depending
on the MOSFET. Unfortunately, the high input impedance causes static problems
and other handling problems.
This webpage will only discuss MOSFETs as used in a switching application.
Linear application of MOSFETs will not be discussed (unless I get real
real bored).
H-Bridges
A H-bridge is used to control a DC motor. It allows the motor to start
and stop and most importantly to reverse direction. In order to reverse
the direction of a DC motor, the current through the DC motor must be reversed.
This basically boils down to swapping the motor leads electronically -
not an easy task to do successfully!
Unfortunately, there is an early explanation of the H-bridge that
is circulating dated pre-Jan 1996 that does not correspond to these schematics.
The original files were lost in a hard-drive crash. Please use only the
schematics shown here with the corresponding circuit descriptions. It will
save you lots of confusion.
Here are examples and explanations of
MOSFET Switchs
The following information is still valid for using MOSFET's as switches to
control DC motors (April 2001):
Discussion
on Pulse Width Modulation Limitations
I have had many enquiries on pulse width modulations (PWM) frequency
limitations of the supplied circuits. The limitation on the maximum PWM
frequency is most likely due to the secondary MOSFET receiving its turn-on
voltage based on one side of the DC motor. The DC motor is an inductive
device and will contribute to the circuit as a low pass filter (LC). This
will limit the turn-on frequency of the secondary MOSFET (low-side). It
will probably heat up the secondary MOSFET and eventually burn-it out at
higher frequencies. This could happen very quickly.
Solution:
Use an invertor on the logic inputs and add another drive transistor
to each of the secondary MOSFETs. This way, all MOSFET gate voltages are
isolated from the induction caused by the DC motor. Here is a simple example
circuit using
two digital inputs.
Modified P-ch & N-ch MOSFET H-bridge using a
single supply, P-channel and N-channel FETs for PWM application
There could be problems with the upper transistor and lower
transistors on each side
conducting while changing state. Ideally, you would have a separate digital
input for each mosfet and turn off all
the mosfets before changing state as shown at
index.html.
Things to watch for:
Each DC motor/circuit is going to have very different characteristics.
Make sure that all MOSFETs are off before changing state. The off period
will vary depending on the circuit's characteristics. Trial and error method:
start with a long off period between changing states and start shortening
it. If you have a scope, you should be able to measure the actual turn
off time of the motor. Probably, the motor will generate back emf until
it physically stops. This again depends on the physical load (inertia)
of the system.
I've only tested the supplied circuits for forward, backwards and stop.
Straight DC control. So if its successful and you want to share your
experience,
email me.
TIPS
- Gary Crum suggested that,
instead of slowing gate rise time to mute noise, run the output of your
H-bridge through (depending on load)
some inductors in the 40uH to 100uH range; he has found this quite useful,and
it keeps the FETs cool.
Place the inductors in series with the motor, as close to the FETs as
possible - this will mute noise that otherwise fouls encoders and control
circuits.
Try DALE #TJ6-IU-100: this is a 100uH 15 to 20 amp toroidal choke that is
adequate for a 1.5KW 180VDC application.
For smaller motors, say 0.5KW, try a Prem Magnetics SPB-300, 40uH @ 12A (i
think).
Prem is near Chicago, call (815) 344-6385.
This site is sponsered by
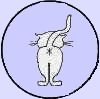
Cat's Ass Kustoms
Parts, Performance, Passion News for Motorheads
|
Disclaimer: The circuits described here are for reference purposes only. There is no guarantee in any way shape or form that they will work for your specific application. Use them at your own risk.
Please send any corrections, suggestions or errors that you may have
caught to me.

Copyright Eugene Blanchard Jan 2007
|
|